Overview
Modern locomotives rely heavily on stable electrical systems, not just for starting, but also for powering critical onboard electronics, safety systems, hotel loads, and battery management systems. One overlooked factor that can compromise this reliability is charge ripple - fluctuations in voltage that occur during battery charging cycles. These ripples, often caused by inconsistent load conditions or suboptimal charging profiles, may seem minor in magnitude but can have major consequences over time.
For a leading Class 1 railroad operating in harsh environments and with high service expectations, ripple voltage was becoming a concern. The fluctuations introduced by frequent engine starts, variable loads, and aging electrical components were putting undue stress on batteries and sensitive electronic systems. This not only increased the likelihood of electrical noise and data disruptions but also accelerated battery degradation leading to costly replacements and unexpected downtime.
To address these concerns, the railroad turned to ZTR and its KickStart Battery and Starting Manager (BSM), a supercapacitor-enhanced solution built not only to assist with starting reliability but also to improve overall electrical health. A key feature of BSM, ripple voltage reduction, was put to the test in a targeted pilot program aimed at stabilizing bus voltage and enhancing power quality across the locomotive’s electrical ecosystem.
The Class 1 railroad in question faced a growing concern with the instability of bus voltage during charging cycles, specifically in the form of high charge ripple. Although often overlooked, charge ripple, small but rapid voltage fluctuations during battery charging, can have far-reaching effects on locomotive performance and reliability.
In this case, pre-installation data showed ripple voltages averaging around 0.397 volts, which while within typical tolerances, still introduced significant electrical noise across the system. Over time, these fluctuations can:
- Accelerate battery wear, reducing battery lifespan and leading to frequent, costly replacements
- Disrupt electronic control systems, increasing the risk of false fault reporting or communication errors
- Create inefficiencies in charging, undermining the effectiveness of idle-reduction systems like AESS (Automatic Engine Stop-Start)
For a railroad operating in demanding service conditions, these effects translated to higher maintenance costs, increased risk of unplanned downtime, and added strain on their sustainability goals.
The railroad needed a solution that not only provided cranking support to eliminate dead-won’t-start events, but also one that could actively stabilize the electrical environment onboard the locomotive, improving battery health and extending system longevity without requiring significant hardware changes.
To address the challenge of excessive charge ripple and its negative effects on battery performance, a Class 1 railroad implemented the KickStart Battery and Starting Manager (BSM) on a test locomotive. KickStart BSM includes a dedicated Power Manager Module that regulates how energy flows into the batteries.
Rather than allowing raw or inconsistent power delivery from the charging system, the Power Manager smooths voltage fluctuations by using active filtering and intelligent control algorithms. This leads to significantly reduced charge ripple helping protect battery health and ensure longer lifespan. The implementation required no major overhaul of the existing locomotive systems, making it an efficient and scalable solution for addressing charge-related stress.
The deployment of KickStart BSM led to a measurable and significant improvement in charging voltage stability, specifically, a substantial reduction in charge ripple, which is a critical factor influencing battery longevity and electronic reliability.
Before BSM was activated, the locomotive experienced high levels of charge ripple during battery charging operations. The ripple component fluctuated widely from -0.2 V to +0.2 V, creating a noisy charging environment. This variability resulted in a standard deviation of 63 mV, indicating a highly unstable voltage profile during the battery charging process.

Upon activation of KickStart BSM’s battery charging function, the ripple component was significantly stabilized. Post-activation data showed that fluctuations were limited to a narrow range of -0.02 V to +0.02 V, with the standard deviation reduced to just 8 mV. This represents an 87% reduction in charge ripple, comfortably surpassing the industry benchmark target of 80%.
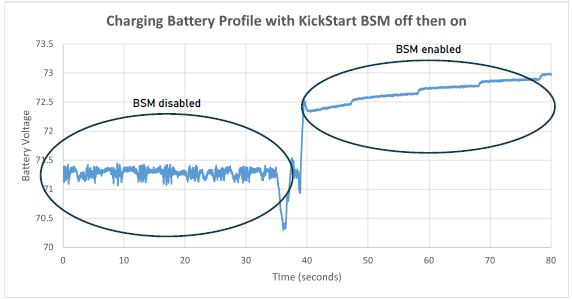
The improvement is visually evident in the comparative voltage graphs, where the noisy, jagged pattern during the BSM-disabled phase gives way to a much smoother and consistent voltage curve once BSM is enabled. This stability ensures that batteries are charged in a healthier manner, minimizing stress on the cells and reducing long-term degradation.
By virtually eliminating harmful ripple during charging, KickStart BSM not only enhances battery performance and life but also contributes to more reliable locomotive operation, especially in harsh environments where consistent electrical performance is critical.